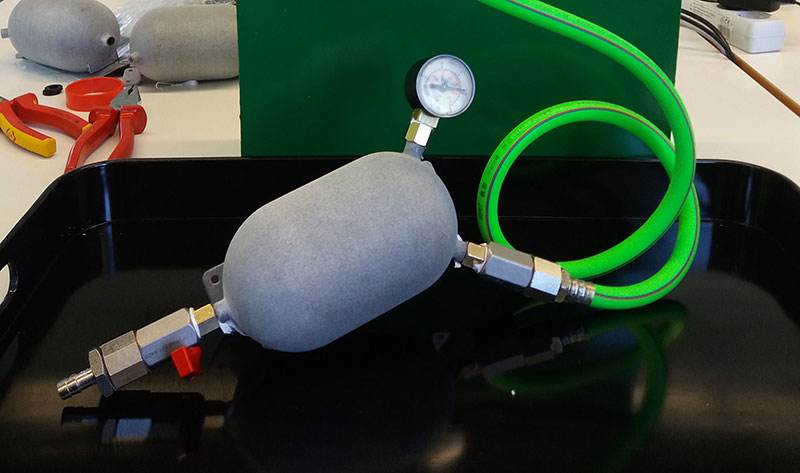
Pressure vessel production with HP Multi Jet Fusion
industrialpartners offers its customers the most innovative processes for the production of small and medium sized medium part series. In addition to conventional injection moulding, we also use the latest 3D printing processes for the production of our parts – such as Multi Jet Fusion Technology (MJF) from HP.
This revolutionary 3D printing process has many advantages over conventional laser sintering. Parts produced with HP MJF have a higher density, an eroding-like surface structure and can be produced in the shortest production time.
This means for you: No series production of plastic parts and assemblies on an industrial scale at attractive prices!
To expand our product range, we have now conducted an internal study to determine whether economically viable pressure vessel production with HP MJF is possible. Our question in this study was therefore: “Is the HP Multi Jet Fusion manufacturing process suitable for the production of tanks that are exposed to high internal pressure?
We produced a few tanks for this purpose and then tested the resulting containers. For the pressure-tightness test, the test specimens manufactured with HP MJF were filled with water and permanently pressurized to 20 bar for four months using a hand pump.
The result for an additive manufacturing process is astounding: no moisture leakage and no pressure loss – even over a long period of time!
If one compares the pressure vessel production with HP MJF with other processes in which, for example, conventional vessels are produced from metal or conventional plastic production processes, there are significant advantages for this process:
With HP MJF, tanks can be manufactured in any shape (e.g. spherical, cylindrical or cube-shaped) that guarantees high wear resistance and thus suitability for use on an industrial scale. The pressure vessels produced in this way can be used for different pressure ranges depending on the wall thickness dimensioning. Due to the process-related easy scalability, freely selectable design and the possibility of integrating different coupling pieces in one production step, the production of complex tanks and pressure vessels, for example, is no longer a problem. In addition, pressure vessel production with HP MJF as an alternative to conventional processes remains comparatively inexpensive!
In a separate study by HP, it was also demonstrated that parts produced using the MJF process have a higher density (1.01 g/cm³) than parts produced using conventional laser sintering (0.90-0.95 g/cm³). The polyamide HD 3D PA 12 used in the MJF also has a much lower porosity than the SLS PA 12 material commonly used in the laser sintering process. It enables the production of ultra-thin layers of only 80 micrometers and thus excellent detail accuracy as well as outstanding surface quality. It also scores well in terms of chemical resistance: Even hot water, alcohol, aliphatic hydrocarbons (including gasoline components), engine oil and DOT-3 brake fluid cannot harm the PA 12 material used by Multi Jet Fusion. But that’s not all: The pressure vessels created with HP MJF have also passed IP66 and IP67 tests.
Conclusion: HP revolutionized pressure vessel production with the Multi Jet Fusion process and we
are proud to be able to offer this new technology to our customers!
For further information, two documentations are available.